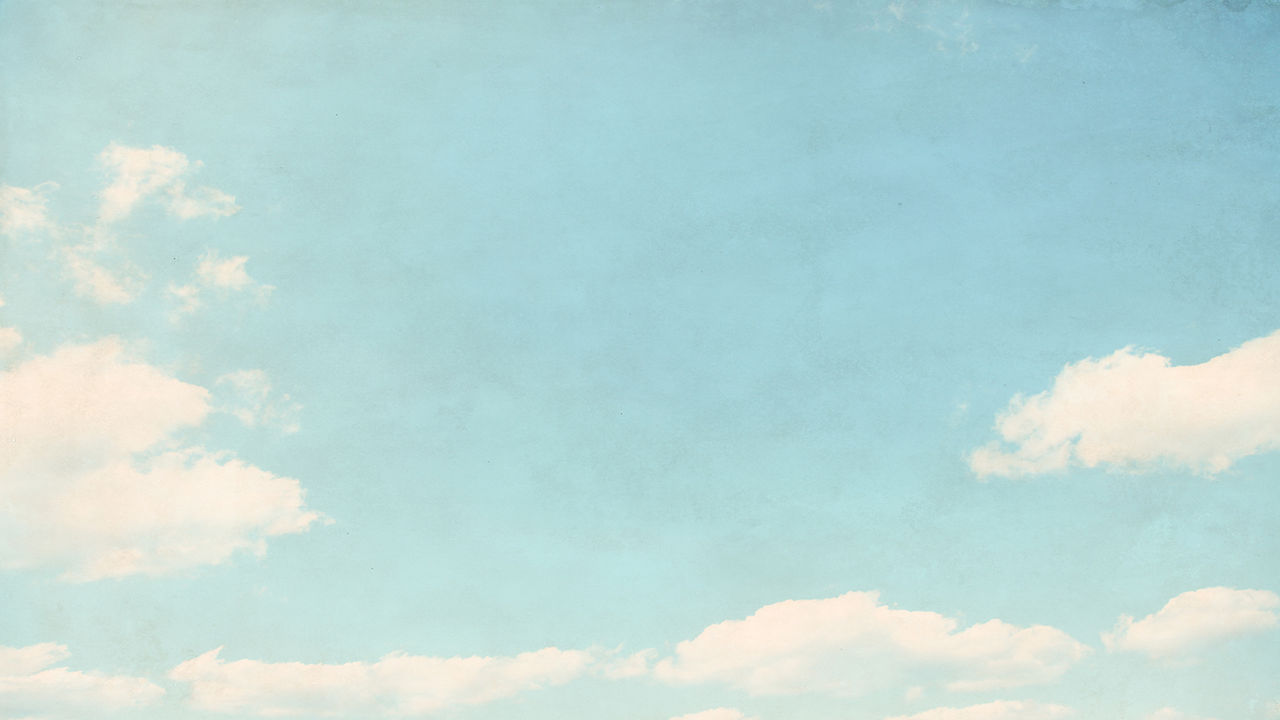
Fuel The World
First-generation biofuels are fuels produced directly from food crops. The first generation biofuel is the earliest and most widely used biofuel among the other three generations of biofuels. It has a more developed technology, relatively simple production, and infrastructures already in place making it easy to be commercialized. The main first generation biofuels are bioethanol, biodiesel and biogas.
First Generation Biofuel
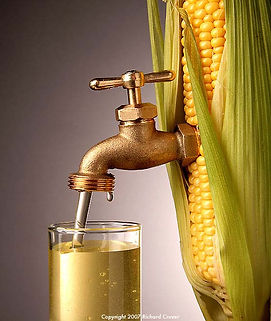
[6]
(6)
Bioethanol
Bioethanol, C2H5OH, also known as Ethanol or ethyl alcohol, is a clear alcohol made from energy crops that are generally high in sugar or starch. These energy crops used for bioethanol production are grown depending on each country’s agricultural strength, for example corn in USA and sugar cane in Brazil. Bioethanol which is made from organic material is different from the

synthetic ethanol, a petroleum byproduct. It is one of the most widely used substitutes for petroleum in transportation as gasoline engine can run on bioethanol blend without much modification needed.
(7)
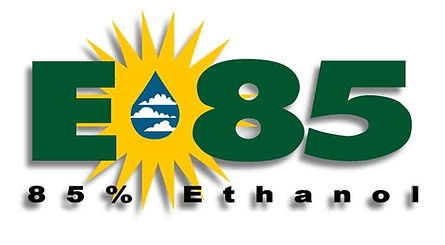
(8)
The most widely used blend is a mix of 10 percent ethanol and 90 percent petrol called E10 because this blend requires no modification on vehicle engine. There is also E85 which is a blend of 85 percent bioethanol with 15 percent of petroleum. This blend can only be used by Flexible Fuel Vehicles (FFV), vehicles that have specially designed or modified engines to run on regular fossil fuel, bioethanol, or both.
The bioethanol blend has the advantage of
being more efficient and has better performance than conventional fuels with its higher octane rating. In addition, the ethanol blend can oxygenate fuel and help fuel burn more thoroughly, therefore reducing pollution emission. Furthermore, bioethanol is environmentally friendly because it burns to produce carbon dioxide and water which can both be absorbed by plants. It is also biodegradable and low in toxicity as it is a natural product. Therefore there will be no negative environmental impact when spilled.
[7]
[8]
{2}
Economic Impact
Bioethanol and FFV have already been widely used in United States and Brazil, the two countries that produce the most ethanol in the world. In 2013, around 1040 million m3 of bioethanol are produced globally and around 80 percent of the bioethanol is used as fuel. The United States alone produced 518 million m3, almost half of the total global bioethanol production. Ethanol accounts for more than 90 percent of all biofuel in United States, making it one of the most important parts of biofuel in the United States. The United States and Brazil are also the leading countries pushing for using bioethanol as a substitute for petroleum. There are around 8 million FFV in the United States that are currently on the road and more than 90 percent of new cars registered in Brazil are FFV. Brazil also requires that all gasoline must contain a minimum of 20 percent ethanol. In 2010, the federal government received an estimate of $8.6 billion and the states received revenues which totaled $4.8 billion from the economic activity stimulated by the U.S. ethanol industry. In addition, the ethanol industry bought around $18 billion in corn which brings the direct income impact of $448 million to the agricultural sector and billions of dollars of indirect impact. In 2013, the U.S. ethanol industry helped support nearly 390,000 jobs and contribute more than $44 billion in GDP.
[9]
[10]
How is Ethanol made?
The most common ways of turning plants high in starch or sugar into ethanol are dry milling and wet milling. The wet milling process uses corn more thoroughly than dry milling, and extracts higher value from each part of the corn kernel. However, wet milling yields less ethanol compared to dry milling, as some of the fermentable starch is attached on the many byproducts. Dry milling has the advantage of being less capital intensive and has a lower operating cost.
In dry milling, the plants are first grounded into flour and water is added to make into mash. Enzyme will then be added to the mash for enzymatic hydrolysis to take place. The glucoamylase enzyme will break the starch molecules into fermentable sugar (glucose). Next, yeast is added to the mash that is now mostly sugar. The yeast through the process of fermentation will then turn the sugar into ethanol and carbon. Following the fermentation, the mash is distilled and separated into the ethanol that will be used as fuel and stillage that can be turned into nutritious livestock feed. The other byproducts of making bioethanol are also being put into use. For example, the carbon dioxide is captured and sold to carbonate soft drinks or to make into dry ice.
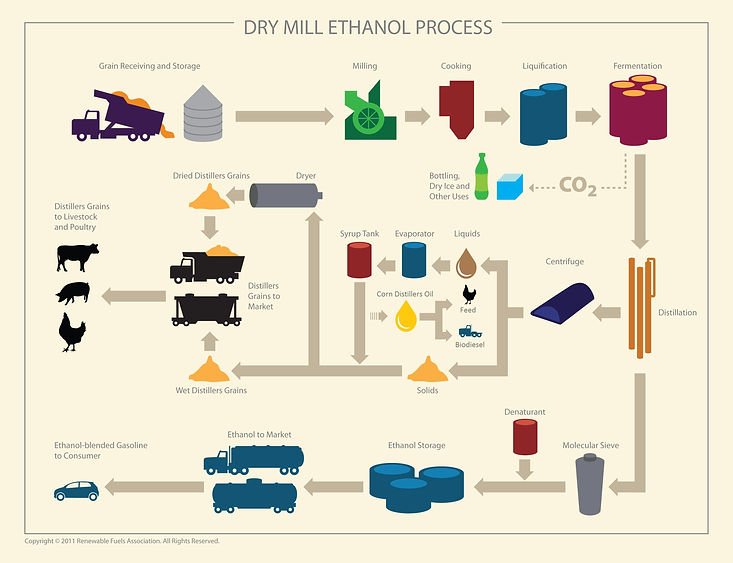
(9) The image shows the many steps of dry milling process of ethanol and the byproducts of dry milling including livestock feeds and carbon dioxide that can be make into dry ice or used in soft drinks,
In wet milling, corn kernels are first steeped in a solution of water and sulfur dioxide to help separate the corn into different components. Then, the germ from the corn kernel is removed for a further process to extract corn oil. After the germ removal, the remaining fiber of the kernel is combined with the concentrated steep liquor and is usually made into corn gluten livestock feed. The remaining starch and water then can be turned into ethanol through fermentation similar to the process in dry milling.
In addition to the more traditional dry milling and wet milling, manufacturers have used new technological innovations such as fractionation, low heat fermentation, high gravity fermentation, high temperature yeast, and quick steeping to maximize production and reduce cost and environmental impact.
[11]
[12]

(10) This image shows the different process the mash can go through to create different products.
{3}
Biodiesel
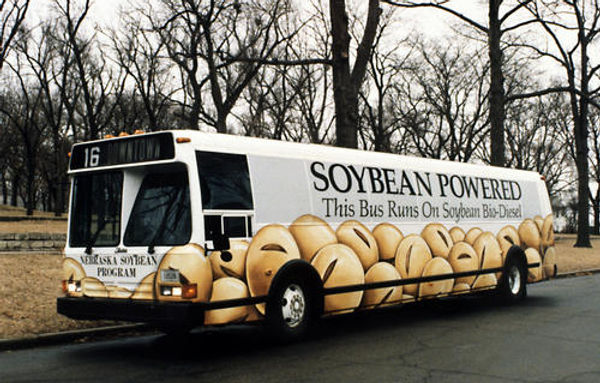
Biodiesel is fuel made from oil and fat such as vegetable oil, animal fat and recycled restaurant grease. It has lower emission and toxicity and is biodegradable and renewable. Biodiesel can reduce greenhouse gas emissions from 57 percent to 86 percent depending on the blend. For example, biodiesel B100 has a 78 percent lower carbon dioxide emission than regular petroleum diesel and the more common biodiesel blend B20 has a 15 percent fewer greenhouse gas emission compare to petroleum diesel. Biodiesel is also safer to handle having a significantly higher flashpoint compare to regular petroleum fuel. This makes biodiesel less likely to combust during handling and transportation. One of the greatest advantages is that biodiesel is similar to petroleum diesel allowing most diesel engine to run on B20 and lower concentration blend with no modification needed. However, some engine modification is needed for regular cars to run on higher concentration blend with some modification.
(11)

(12)
The most common blend of biodiesel is the B20. The B20 is the blend of 20 percent biodiesel with regular petroleum diesel. It is most common for its good balance of cost, chemical property, performance in cold weather, and emission. B20 does have a slightly higher cost compared to petroleum fuel, about 30 cents higher per gallon. Bioethanol crystallize in extremely cold weather therefore the lower the percentage of bioethanol in the blend causes fuel to perform better in cold weather. Bioethanol also have slightly less energy compared to petroleum diesel,
about an difference in 8 percent per gallon. Therefore the B20 blend has about 1 percent less energy per gallon which is almost unnoticeable. Engines running on B20 have similar fuel consumption and horsepower compare to engine running on petroleum diesel.
[13]
Economic Impact
The biodiesel industry has grown steadily with increasing number of commercial production facilities over the past few years. In 2011 it reached the milestone of one billion gallons of production and in 2013 increased to 1.8 billion gallons. The biodiesel supported an estimate of more than 62,200 jobs nationwide. The economic impact of biodiesel increased from $1.4 billion annually in 2006 to $10.6 billion in 2012 supporting more than 50,000 jobs.
[14]
How is Biodiesel made?
Biodiesel is made through a process called transesterification that converts feedstock that contains oil into burnable fuel. The most common feedstock for biodiesel are plant oil; oil from plants like soybean, canola, palm, cottonseed, sunflower and rapeseed. Other feedstock includes recycled animal fat and used cooking oil.
Before the plant oil or cooking oil go through the transesterification, they first have to be heated to dry up the excess water, and then sent to refinement process to remove debris. After the distillation and refinement, the purified oil is sent to transesterification. In transesterification, the oil is mixed with methanol or ethanol in the presence of other catalysts under high temperature to produce biodiesel(methyl ester when methanol is used and ethyl ester when ethanol is used) and glycerin. The glycerine as a byproduct of biodiesel production can be used in cosmetics, hair care and other industries.
[15]
[14]
{4}

(13)
Renewable Diesel
Renewable diesel, also known as green diesel or second generation biodiesel, is made from the same high-end oil biomass as biodiesel. The difference between renewable diesel and biodiesel are the different processes the biomass goes through to become fuel. While biodiesel goes through transesterification, the renewable diesel goes through other methods such as hydrotreating and thermal conversion. The hydrotreating can be done with already existed machineries in petroleum refineries. In hydrotreating, the feedstock will react with hydrogen and catalyst and create renewable diesel and propane. The renewable diesel is chemically similar to petroleum diesel so it can be used in different proportions blended with petroleum diesel.
[16]
Biogas, also known as swamp gas, landfill gas, or digester gas, is gas produced from anaerobic digestion of organic matter including livestock manure, municipal wastewater solids, food waste, fat, and grease. The bacteria decompose the waste material and produce gas that is 50% to 80% methane and 20% to 50% carbon dioxide. This gas can be used to generate electricity and heat without much processing. The biogas can also be processed to be purer and used as alternative fuel for natural gas vehicles.
Biogas has several advantages. For farmers,
running a biogas recovery system with animal manure allows
Biogas

them to have their ownheat and electricity supply. The digested manure or wastes are high quality fertilizer, mulch, and potting soil. Biogas production can also greatly reduce water contamination and odor pollution. For landfills and animal manure, methane that is otherwise emitted into atmosphere as greenhouse gas can be turn into useful fuel through biogas production. As landfills gas is the third largest source of human methane emissions in the United States, biogas production greatly reduced the methane in atmosphere.
[17]
[18]
(14)
How is biogas made?
Biogas is produced through a biological process called anaerobic digestion. Anaerobic digestion is the process which microorganism breaks down organic material in an oxygen free environment.
The process of anaerobic digestion consists of four steps and each is carried out by different groups of bacteria. The first step is hydrolysis, where larger organic polymers such as carbohydrates and fats are broken down into smaller compounds including simple sugars and amino acids. This process makes the materials available to other bacteria. Next, in the second stage called acidogenesis, acidogenic bacteria breaks down sugars and amino acids into carbon dioxide, hydrogen, ammonia, and organic acids. Then, in the third and fourth step, acetogenesis and methanogenesis, Acetogenic bacteria produce organic acids and methanogens turn it into methane.
In animal manure digester, the anaerobic digestion are usually done in tanks for oxygen free condition. The materials are constantly stirred and heated for homogeneity and consistent of gas. For small scale farms, a simple plug-flow digester could process 8,000 gallons of manure per day, generating more electricity than can be use by the farmers. The plug flow digester consists of a manure collection system, a mixing pit and the digester. It is a rectangular container covered with an airtight cover.
{5}

(15)
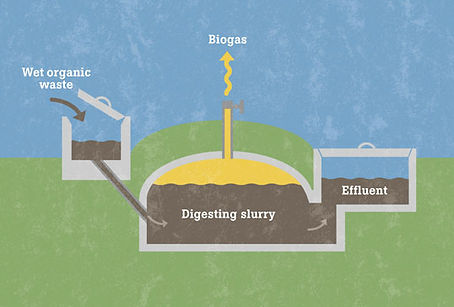
The landfill biogas occurs naturally in landfills underground from uncontrolled biomass decay. The landfill biogas production efficiency is determined by the composition of the waste material, humidity, temperature and other factors. The landfill must be at least 40 feet deep and have at least one million tons of waste for the production to be feasible. The produced biogas is collected through a series of wells drilled into the landfill and filtered to remove impurities.
(16)
[19]
[20]
Economic Impact
There were about 180 operation biogas recovery systems in United States in 2011, producing enough electricity to power 47,000 homes. In 2010 EPA estimates that about 8,000 farms in U.S., can support the biogas recovery systems to produce 1,6000 megawatts and to reduce 1.8 tons of methane.
[21]