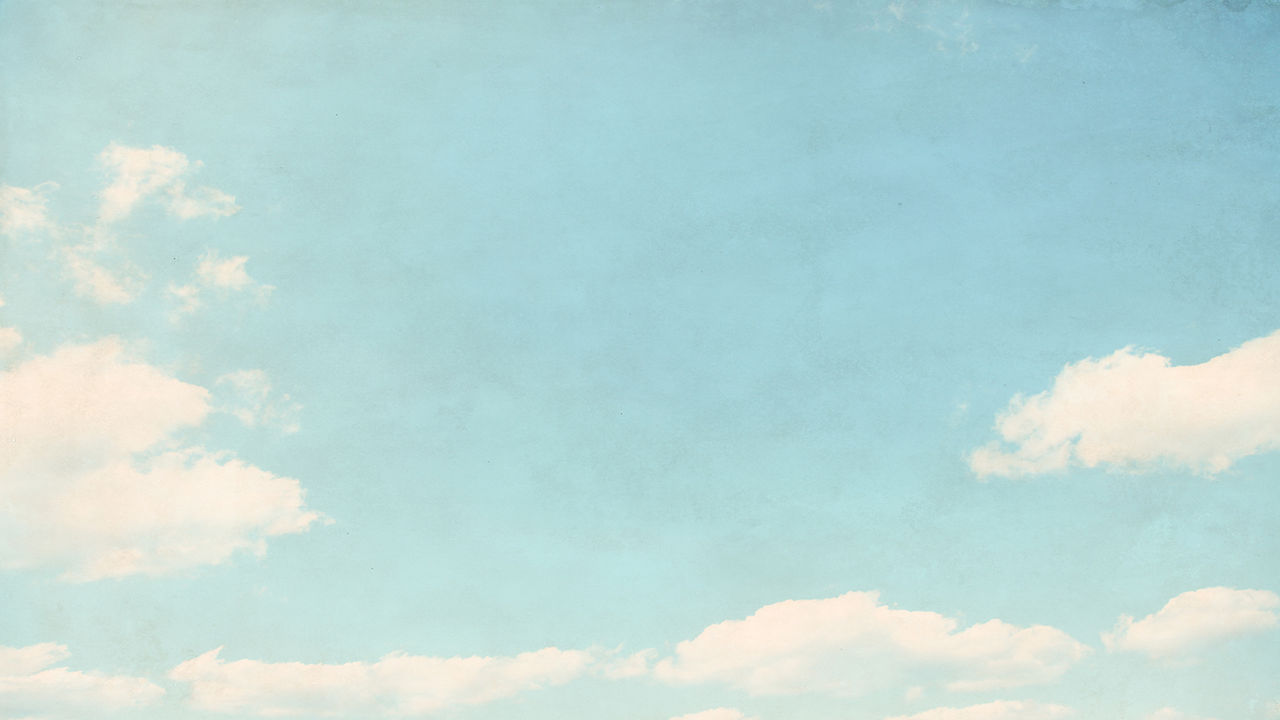
Fuel The World
Second Generation Biofuel
Second-generation biofuels refers to fuel produced from non-food lignocellulosic materials which includes inedible part of food crops. As lignocellulose is the most abundant renewable organic compound on earth, the second generation biofuel has great potential to be cost competitive to current fossil fuel, and can widen feedstock option to produce greater amount of fuel. On top of that, second generation biofuel has several other advantages over first generation biofuel. Second generation biofuel produces fuel without threatening food supplies and biodiversity and it also has a greater yield of fuel per acre of crop and greater greenhouse gas saving. However, current second generation biofuel is still relatively expensive to make as the feedstock requires more processing.
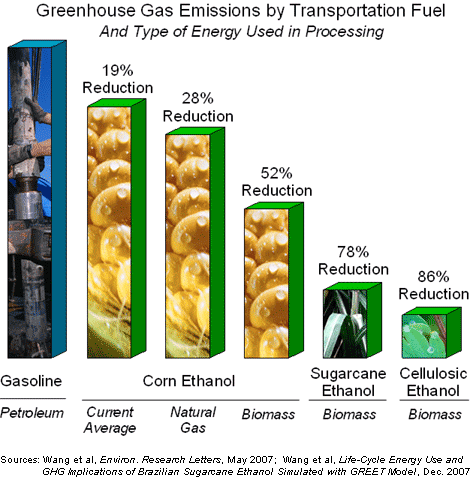
(17)
The second generation biofuel lignocellulosic feedstock can generally be separated into three categories. 1) Agricultural residues such as stems, leaves and husks left behind from food crops 2) forest residues like sawdust. 3) herbaceous and woody energy crops such as grass, switch grass .
[22]
[25]
So what is lignocellulose? Lignocellulose is found in the cell wall and it is mainly composed of lignin, hemicellulose and cellulose. In which the cellulose is a long chain of sugar and hemicellulose is compose of many different sugar monomer. The cellulose and hemicellulose can be turn into sugar then fermented into ethanol but require additional treatments for the resistance of lignocellulose. The challenge of using cellulose as feedstock for ethanol production is the lignin, hemicellulose, and cellulose are tightly bound together.
The pretreatment of the lignocellulose biomass has several purposes. One of the many purposes of pretreatment is to remove lignin from hemicellulose and cellulose as the lignin as a byproduct can be used for heating and many other uses. The pretreatment also disrupts the lignocellulose structure for cellulose and hemicellulose to be accessible for hydrolysis and also reduce the amount of inhibitor that causes crystallinity of cellulose to maximize fuel production. There are many pretreatments for lignocellulose, some already used in commercial production while some are just developed. The pretreatment can be generally separated into four categories- biological, chemical, physical, and physicochemical.
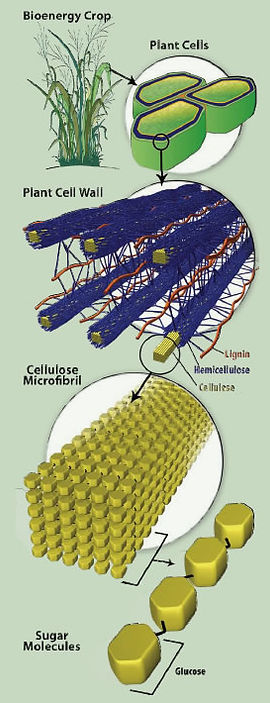

[26]
(19)
Lignocellulose
(18)
Pretreatment
Biological pretreatment
Biological pretreatment uses cellulolytic microorganisms to break down lignocellulose. Fungi that were major decomposer for wood in the ecosystem can produce degrading enzyme to separate lignin, hemicellulose and cellulose. The types of fungi commonly used for biological pretreatment are white, brown and soft rot-fungi. Each type of fungi have its distinct way of decomposing lignocellulose making each type of fungi to have advantage in treating certain lignocellulosic feedstock. These filamentous fungi

are ubiquitous in the environment making biological pretreatment to be eco friendly and cheap alternative. However, biological pretreatment is very slow compared to other pretreatments and harder to manage on a larger commercial scale. Synthetic biologists continue to study and manipulate these microbes used in fuel production hoping to yield artificial biological organisms that is efficient and produce economically viable biofuels.
[23]
(20)
Chemical pretreatment
Some of the Chemical pretreatment are acid hydrolysis, alkaline hydrolysis, organosolv, oxidative delignification, room temperature ionic liquid. The chemical pretreatment uses different chemicals to disrupt biomass structure and make the material more accessible. In acid hydrolysis, there are strong acid hydrolysis and weak acid hydrolysis. Strong acid hydrolysis use corrosive acid like H2SO4 and HCl to remove lignin and hemicellulose and often no subsequent enzymatic hydrolysis is required. However, strong acid hydrolysis do require an extra step of extensive washing and detoxification before it goes into fermentation and it also takes more time compared to weak acid hydrolysis. Weak acid hydrolysis uses diluted or weak acid like sulphuric acid for hydrolysis of hemicellulose but weak acid has little to no lignin. Therefore, weak acid hydrolysis works best on biomass with lesser lignin. Both strong acid and weak acid pretreatment have been commercialized and widely used for treating lignocellulosic feedstock. Alkaline pretreatment uses base such as calcium or sodium hydroxide or ammonia to remove lignin from biomass. It has a lower reactor cost compare to acid treatment. Organosolv uses a mixture of organic solvent (ethanol, methanol, acetone, and ethylene glycol) to remove lignin and improve digestibility of fraction cellulose for enzyme.
[26][27][28]
Physicochemical Pretreatment
Physicochemical pretreatment combines both physical and chemical action to break the structure of lignocellulose and is considered to be more efficient than physical pretreatment. It includes steam explosion, ammonia fiber explosion, CO2 explosion, liquid hot water and many others.
Steam explosion is one of the most applied pretreatment methods because of its low use of energy and chemical. This pretreatment gives complete sugar recovery, requires low capital investment, and has low environmental impact. First in the steam explosion, high pressure steam is injected into a container full of biomass and acid catalysts. The temperature will suddenly rise to 190°C to 270°C and the pressure dropped. As a result, the hemicellulose solubilized and can be hydrolysed by the acid catalyst and cellulose carbohydrate linkage is broken down making cellulose easier to be turn into ethanol by enzyme.
Ammonia fiber explosion uses a lower temperature, 60°C to 100°C, to vaporize liquid ammonia and cause pressure to drop to then cause biomass to swell. The swelling will disrupt bonds in the lignocellulosic biomass and make the biomass easier for enzymatic attack.
Liquid hot water uses water at high temperatures to cause disintegration of the lignocellulosic biomass. This process makes hemicellulose soluble and can be removed almost completely separating hemicellulose and cellulose from one another and avoiding formation of inhibitor.
[26][27][28]

(21)
Physical pretreatment
Physical pretreatment is used generally to reduce the size of feedstock to increase the surface area so a greater amount of cellulose can be converted. Some of the common physical pretreatments are chipping, shearing, milling and grinding. The more complex physical treatments include pyrolysis, gasification, and torrefaction. Pyrolysis, gasification, and torrefaction are all considered thermochemical conversion.
Pyrolysis is a thermal decomposition of biomass in the absence of oxygen. Product of pyrolysis are biochar, oil, and the producer gas (carbon monoxide, hydrogen and methane) and the proportion of each product depends on the temperature used during pyrolysis. The lower the temperature, around 450 °C, more biochar are yielded and in higher temperatures, around 800 °C, more producer gases are yielded. In an intermediate temperature and high heating rate, more bio oil is yielded. The bio oil can not yet be used as fuel for engine directly.
Gasification is similar to pyrolysis but taken to the next step, creating syngas that can be further processed into fuel, chemical, and fertilizer. Gasification can be separated into four steps, drying, pyrolysis, reduction and combustion. In drying, the water is driven off from the biomass and in pyrolysis the biomass starts to decompose at the temperature of 240 °C. The biomass at high temperature of pyrolysis is turned into tar (gas and liquid) and char (solid). In reduction, oxygen is removed from the tar making the gas combustible and in combustion the undesired part are burned leaving behind the product syngas.
Torrefaction is similar to pyrolysis carried out in absence of oxygen, but at a lower temperature of 200°C to 300°C creating solid biofuel that can be use for gasification.
[24]
[25]
[29]
[31]
{6}
{7}
After the pretreatment, the cellulose will be hydrolysed into sugar through a process called saccharification. Other than the acid and alkaline hydrolysis mentioned above there is also the enzymatic hydrolysis which have the potential of having lower cost and higher sugar yield. The enzymatic saccharification use microorganisms produced enzymes called cellulase to hydrolyse cellulose. There are many types of cellulase and often a combination of cellulase will be used to work in synergy to maximize the sugar yield.
[30]
Methanol
Methanol (methyl alcohol), also known as wood alcohol, is methyl alcohol, CH3OH. It acquired the name of wood alcohol because in the past it was extract as a byproduct from wood through pyrolysis. Biomethanol can be made from plants, landfill gas, and many other renewable biomass. Currently methanol is mostly extracted from natural gas because biomethanol is still relatively expensive to make with the costly technology such as biomass to liquid or syngas. However, biomethanol has the advantage of having lower greenhouse gas emission than natural gas derived methanol.

Other Fuels
[32]
(22)
Biobutanol
Biobutanol, butyl alcohol, is a 4 carbon alcohol that is usually used as industrial solvent in many wood finishing products, but can also be blended with other fuel to power conventional gasoline vehicles. It can be used to oxygenate and blend with gasoline in up to 16 percent concentration resulting same amount of oxygen content as 10 percent ethanol blend. Biobutanol is produced from same feedstocks as bioethanol such as corn and sugar cane. Biobutanol has a higher energy content of 10 to 20 percent lower than gasoline compare to the 30 percent lower energy content of ethanol. In addition, biobutanol has a low vapor pressure making it easy to be blended with gasoline. Biobutanol can be produced with existing ethanol production facility allowing dramatic increase in biobutanol production. Biobutanol’s high heat value, high viscosity, low volatility, high hydrophobicity, less corrosive gives it the potential to be a good fuel in the future.
Biogasoline
BIogasoline is a hydrocarbon fuel similar to biodiesel but different structure. Since biodiesel is created for the purpose to substitute for diesel fuel, it has the same linear chains of carbon as petroleum diesel. This is the same for biogasoline. As biogasoline is created to substitute for gasoline, it has the similar shorter branched carbon atom chain like gasoline. The biogasoline is created to match the chemical, combustion and kinetic characteristics of petroleum gasoline while having a higher octane levels. These characteristic of biogasoline allow it to be used in any concentration and not have to modify the internal combustion engine. Biogasoline can be achieved with different processing technology such as hydrotreating and enzymatic process. While biogasoline has many advantages, the current production techniques and production cost prevents biogasoline to commercialize.
[34]
[35]
Fischer-Tropsch diesel
The Fischer-Ttropsch process, a key part of gas to liquid fuel conversion, is a collection of chemical reaction that converts biomass into carbon monoxide and hydrogen then into liquid hydrocarbons that can be used as fuel. It is comprised of gasification, conditioning of syngas and subsequent synthesis to liquid biofuel. The process was developed in 1920s and was mainly used to produce fuel from coal or natural gas. The process using biomass as feedstock is still under development. The process can convert any type of biomass including cellulosic feedstocks. The Fischer-Tropsch diesel produced is similar to fossil diesel with its energy content, density and viscosity, allowing it to be blended with fossil diesel in any proportion without requiring modification of engine or infrastructure.
[33]

(23)